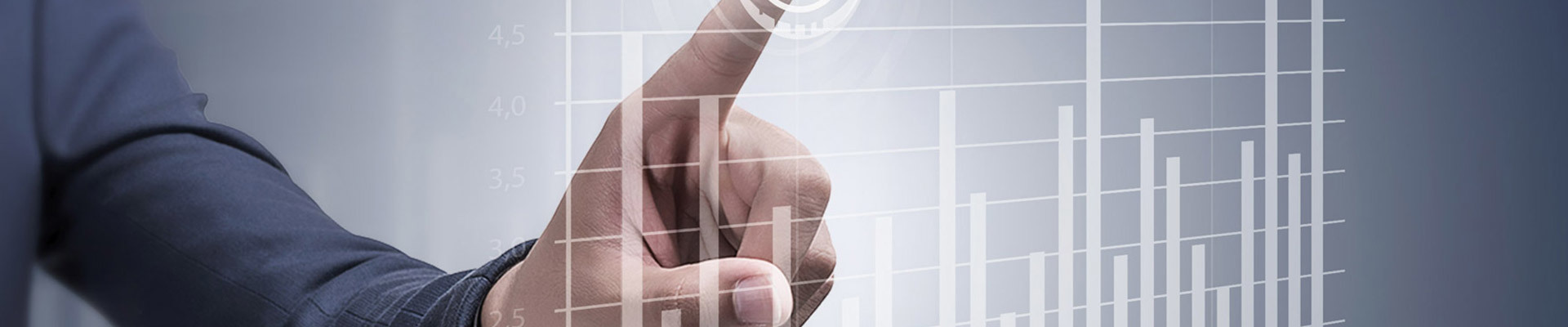
Quality and Integrity Report
2025-07-09
Source:
Jiaxing Fuqiduo Temperature Control Bed Co., Ltd.
Quality and Integrity Report
Report Date: May 2025
Contents Record
I. Preface…………………………………………………………………………(1)
(1) Compilation Instructions……………………………………………………………………(1)
(2) General Manager's Letter…………………………………………………………………(1)
(3) Company Profile……………………………………………………………………(2)
II. Enterprise Quality Management…………………………………………………………………(3)
(1) Enterprise Quality Philosophy………………………………………………………………(3)
(2) Quality Management Organization………………………………………………………………(3)
(3) Quality Management System………………………………………………………………(4)
(4) Quality and Integrity Management………………………………………………………………(6)
(5) Corporate Culture Construction………………………………………………………………(10)
(6) Enterprise Product Standards………………………………………………………………(11)
(7) Enterprise Metrology Level………………………………………………………………(17)
(8) Certification and Accreditation Status………………………………………………………………(18)
(9) Product Quality Commitment………………………………………………………………(19)
(10) Quality Complaint Handling………………………………………………………………(19)
(11) Quality Risk Monitoring……………………………………………………………(19)
III. Outlook……………………………………………………………………………(20)
I. Preface
(1) Compilation Instructions
This report is the first publicly released "Enterprise Quality and Integrity Report" of Jiaxing Fuqiduo Temperature Control Bed Co., Ltd. (hereinafter referred to as "the Company"), which is compiled in accordance with the provisions of the national standards of the People's Republic of China GB/T 29467-2012 GB/T 29467-2012 "Implementation Specification for Enterprise Quality and Integrity Management" and GB/T 31870-2015 "Guide for Writing Enterprise Quality Credit Report", combined with the Company's 2024 quality and integrity system construction.
The Company guarantees that the information contained in this report on quality management, product quality responsibility, quality and integrity management, etc., in terms of concepts, systems, measures taken and performance achieved, does not contain any false records or misleading statements, and assumes responsibility for the authenticity and accuracy of its content.
Report Scope: Jiaxing Fuqiduo Temperature Control Bed Co., Ltd.
Report Period: January 2024 1 to 20 December 31, 2024
Report Release Cycle: 1 time/year
Report Data Description: The data involved in the report comes from the company, and the data is true and valid.
How to Obtain the Report: Company website (www.fuqiduo.cn)
(2) General Manager's Letter
Respected government market supervision (quality supervision) management departments, friends and colleagues from all walks of life:
Jiaxing Fuqiduo Temperature Control Bed Co., Ltd. sincerely thanks the users from all walks of life for their love, support and cooperation!
Our company has advanced production technology and equipment, and has established a strict quality control system.
The company adheres to the "truth-seeking, pragmatic, trustworthy, and innovative" business philosophy , diligent learning, pioneering and innovating, pursuing a healthy and beautiful life ” of enterprise core values , improving the quality of sleep for the masses, promoting scientific and technological progress, creating social value, and achieving corporate profits of mission , constantly providing safe, environmentally friendly, rich, and reliable high-quality products to our users.
Since its establishment, the company has received the care and assistance of leaders at all levels and friends from all walks of life, and has received valuable support from distributors and suppliers across the country. Here, on behalf of all the employees of the company, I would like to express my sincere gratitude to all the leaders, friends from all walks of life, and new and old customers who have cared for and supported the development of our company!
(3) Company Profile
Jiaxing Fuqiduo Temperature Control Bed Co., Ltd. is located in the beautiful Jiangnan region—Dayun Town, Jiashan County, Zhejiang Province. It is a specialized manufacturer of thermal bedding products and also a high-tech enterprise in Zhejiang Province. Its specialized products have obtained the China National Compulsory Product Certification Certificate ("3C"). The company integrates R&D testing, production operations, and logistics warehousing, with one large-scale production and processing workshop, eight production lines, and two large warehouses. In 2016, the company invested in the construction of a production and processing workshop and a new office building, and the environment has been completely renewed. The company has established a county-level technology research and development center, with a well-equipped laboratory and product testing room. The company has professional R&D personnel 15 people. With the business principle of "patent brand, technological leadership; warm in winter and cool in summer, pursuing excellence", the company continues to increase investment in technological innovation and R&D, and increase the introduction and training of scientific and technological talents. Under the background of increasingly fierce competition, the enterprise has steadily developed. The company has formed a relatively complete design and R&D system, production and manufacturing system, sales channels, and standardized management system.
Over the past fourteen years, the company has been awarded the "Zhejiang Province A-level Contract-Honoring and Credit-Keeping Unit" by the Jiashan County Administration for Industry and Commerce of Zhejiang Province; and the honorary title of "Honest Private Enterprise" by the Publicity Department of the CPC Jiaxing Municipal Committee and the Jiaxing Municipal Administration for Industry and Commerce. In the Jiaxing Brand Power List selection activities in 2013-2014 and 2017-2020, the company has won five honors. As a caring public welfare enterprise, Fuqiduo Company donated funds to build the "Fuqiduo Love School" in Xiuyan Manchu Autonomous County, Liaoning Province, and received the honorary plaque of "Donation for School Construction, Great Love Without Boundaries" from the Xiuyan County Education Bureau. The company also invested in the construction of the Fuqiduo Love Nursing Home in Jiashan County.
Fukui's multi-brand products are novel, of superior quality, and reliable. They are qualified products manufactured with the permission of the national market supervision and administration department, possessing 86 national patent certifications.
In the next three to five years, the company will, with the mission of "improving the sleep quality of the masses and promoting scientific and technological progress, creating social value, and achieving corporate profits ” as its mission, continuously strengthen research and development innovation, and continuously improve product technology levels; promote lean production and manufacturing, continuously consolidating the comprehensive ability to provide high-quality products; integrate resources from all parties, vigorously promote business model innovation and management model innovation, adapt to long-term development strategies, maintain a leading position in the industry; comprehensively enhance the company's overall competitiveness, and become a favored brand of jade beds (mattresses) in the thermal industry. II. Enterprise Quality Management
(I) Enterprise Quality Philosophy
Since its establishment, the company has been committed to creating high-quality products, regarding product quality as the cornerstone of the company's survival and development. The company has successively passed
、GB/T ISO9001 and GB/T45001 management system certifications, and the physical quality of its products has reached the international leading level. Fukui's professionalism, enthusiasm, efficiency, and brilliance, service stars, make you shine even brighter. Fukui not only cares about product quality but also cares about product service. Customer needs are fully met; customer opinions are listened to patiently, tirelessly providing customers with intimate and thoughtful service. 14001 Strictly according to international quality management system standards operation ensuring that the quality of the company's products is strongly guaranteed, thus enabling the smooth implementation of the company's quality policy. In order to fundamentally strengthen quality management and improve the company's operating quality, the company uses the introduction of the excellent performance model as an opportunity to promote total quality management, through internal audits, self-evaluation, third-party audits or evaluations, continuously seeking improvement opportunities and continuous improvement methods, moving towards excellent performance. Since its establishment, the company has never experienced any major quality complaints, and the pass rate has reached 100% in annual inspections by quality and technology departments at all levels. The company publicizes its corporate culture and quality philosophy through meetings, bulletin boards, company websites, and WeChat official accounts.
(II) Quality Management Organization
The company follows the "three no" principles of quality management: do not accept non-conforming products, do not manufacture non-conforming products, and do not release non-conforming products. With a high degree of importance attached to product quality, the company has established a quality manager system, formulated inspection standards for various materials, components, and products, and each department performs its duties, communicates and cooperates with each other, strengthening product quality control from research and development, procurement, and production processes. (Figure 1) Organizational chart
Figure 1: Quality, Environmental, Occupational Health and Safety Management System Organizational Chart
(III) Quality Management System
Since the introduction of the ISO9001 quality management system, the company has taken "pursuing excellence, scientific innovation; customer satisfaction, continuous improvement" as its quality policy. In the design, development, production, and sales processes, it strictly follows GB/T 19001-2016 "Quality Management System Requirements" to establish a quality management system, forming a quality manual, procedural documents, and other quality documents, implementing and maintaining them, and continuously improving to ensure their effectiveness.
1. Quality Management System Policy and Objectives
From the introduction of the ISO 9001 quality management system, adhering to the "safe and reliable, continuous improvement" of product quality, to the introduction of the excellent performance management model, promoting total quality management, the company has established an integrated total quality management system with strategy as the core and GB/T19580 excellent performance model as the framework, meeting the requirements of six major stakeholders: customers, shareholders, employees, suppliers, society, and partners. Corresponding strategic planning and quality objectives have been established at all levels of the company, and quality assessment KPI objectives and quality accountability systems have been established based on the company's performance assessment system.
1.1 Quality Policy:
Pursuing excellence, scientific innovation; customer satisfaction, continuous improvement
1.2 Understanding of the Quality Policy:
a) Emphasizes that product quality requirements must be based on customer and legal requirements.
b) Emphasizes that product quality is designed (including product design and process design) and manufactured based on a thorough analysis of customer requirements and legal requirements, rather than inspected.
b)强调产品质量是通过对顾客要求和法律法规要求的深入分析之后,设计(包括产品设计和工艺设计)并制造出来的,而不是检验出来的。
c) Emphasizes the concept of system management, ensuring product quality through the identification and control of process factors.
d) Records and analyzes process results to identify areas for improvement, implements improvement measures, continuously improves processes, and pursues excellent performance.
1.3 Quality Integrity Policy:
Survival and development through quality, and efficiency through quality.
2. Quality Education
During the operation of the system, the company uses various scientific and effective methods for measurement, analysis, and improvement, based on the PDCA cycle system method for continuous improvement. The company uses various tools to continuously improve the performance of various departments and levels, and adopts benchmarking and learning methods to continuously correct individual work ideas and methods to ensure the achievement of individual and overall company goals. The company actively communicates and exchanges with external parties and invites experts to provide specialized training to company employees as needed. The company regularly conducts quality education for employees at all levels, and conducts specialized management of quality control points to ensure the consistency of product quality in the manufacturing process.
To firmly establish the integrity awareness of all employees, the company formulates an annual education and training plan at the beginning of each year. Department heads, according to company requirements, prepare education and training plans and content, and carefully organize the education and training of their subordinates. Workshop directors are responsible for the integrity publicity and education work of team leaders and employees. The company uses various methods, including specialized training, posting or conveying written materials, exchange of experience of advanced employees in quality integrity, and the use of image displays, to implement quality integrity education for company employees.
3. Quality Regulations and Responsibility System
The company formulates internal related standards by collecting laws, regulations, and other standards and requirements, ensuring that products meet national laws, regulations, and national and industry standards (some indicators exceed external requirements), and practicing social responsibility through product technology. At the same time, the company has formulated the "Annual Quality, Environmental, Occupational Health and Safety Management Objectives", clarifying responsibilities for product quality control, and adhering to the principle of not letting go of quality accidents.
The company has compiled the "Compliance Obligation Identification and Evaluation Control Procedure", actively identifying and collecting laws, regulations, industry and product standards, and regularly evaluating their compliance to meet the requirements and expectations of laws, regulations, and customers.
Table 1: Quality standards and other relevant laws observed by the company
Category |
Content |
Employee Rights Social Responsibility |
《Labor Law》,《Trade Union Law》,《Consumer Rights Protection Law》,《Environmental Protection Law》,《Safety Production Law》,《Occupational Disease Prevention and Control Law》, ISO9001:2015 、ISO14001:20 15 Standard, GB/T45001 standard, etc. |
Product Standards Implementation and Formulation |
GB/19001-2016 Quality Management System Requirements, CNCA-00C-005 Mandatory Product Certification Implementation Rules Factory Quality Assurance Capability Requirements, CNCA-C07-01-2017 Mandatory Product Certification Implementation Rules Household and Similar Purpose Equipment |
The company has formulated the Internal Audit Procedure ", and the "Management Review Control Procedure", and has cultivated an internal auditor team. To ensure the effectiveness and continuous improvement of the system operation, internal audits, process audits, and quality inspections have been arranged. For nonconformities found in the audit, the responsible department analyzes the causes, formulates corrective or preventive measures, implements rectification, and verifies the rectification effect, ultimately forming an internal audit report, proposing suggestions for system rectification and prevention of nonconformities, and serving as an important input for management review, reporting to top management.
The company has formulated the "Nonconforming (Product) Control Procedure" and the "Nonconforming and Corrective Action Control Procedure" to strictly control nonconforming products. All products of the company undergo online inspection before being allowed to flow into the next process or leave the factory. Any nonconforming product has clear requirements for identification, recording, isolation, and handling. All nonconforming products must be re-inspected and qualified after rework or repair before entering the next process.
At the same time, according to the "Product and Service Release Control Procedure", the Monitoring, Measurement, Analysis and Evaluation Control Procedure ", etc., detailed records are kept for all nonconformities, and after statistical analysis by a designated person, the responsible unit formulates corrective and preventive measures according to the "Nonconforming and Corrective Action Control Procedure" and implements rectification. The problem item can only be closed after the effectiveness of the corrective and preventive measures is evaluated.
In addition, the company has also formulated the "Quality Management Manual", the "Internal and External Communication Control Procedure", the "Human Resources, Capability and Awareness Control Procedure", etc., to hold accountable and educate those responsible for quality problems, and in daily R&D and production operations, emphasize systematization, through quality control circles, continuous improvement activities and the application of quality tools, fully applying the PDCA cycle for continuous improvement and the pursuit of excellence.
(IV) Quality Integrity Management
1. Quality Commitment
a) Integrity and Law Abidance
Top leaders follow the "cooperation over competition" management philosophy, strictly abide by the "Company Law", "Economic Law", "Contract Law", "Product Quality Law", "Safety Production Law", "Environmental Protection Law", "Labor Law", and mechanical manufacturing industry-related laws and regulations, strengthen employee legal knowledge training, cooperate with government departments to carry out legal education activities, encourage and commend employees' "positive energy", so that the style of integrity and law-abiding is deeply rooted in the consciousness and behavior of all company employees. The company's contract default rate is zero, it never owes bank loans, overdue receivables are reduced to a reasonable range, senior and middle-level leaders of the company have no records of violations of laws and disciplines, the number of employee violations is zero, and a good credit and moral image has been established among agents, customers, the public, and society.
b) Meeting Customer Needs
The company attaches great importance to technological research and development, strengthens investment in R&D, takes customer needs as the center, actively listens to customer opinions and suggestions on functions, quality, and configuration, carries out product improvement and innovation activities, and meets customer needs for products and delivery times. In terms of product quality, the company strictly implements the ISO9001 quality management system, and guarantees product quality and safety through technological breakthroughs, quality improvement, and QC group activities.
2. Quality Management
--Product Testing
- Product Quality Tracking
- Evaluation is carried out during design and production to improve existing risks and defects;
- Testing is carried out before delivery, and test results are recorded;
- Tracking customer feedback on product quality after delivery;
④Regularly conduct full-project inspections of products;
⑤Conduct product quality surveys in customer satisfaction surveys.
(2) Tracking service quality
①Register customer needs information, conduct follow-up visits after service, and track service effectiveness;
②Collect and analyze service quality information to improve service quality;
③Conduct service quality surveys in customer satisfaction surveys.
--Quality Traceability
The company organizes management review meetings annually to review the suitability, adequacy, and effectiveness of the quality, environmental, and occupational health and safety management systems, achieving continuous improvement of the management system, ensuring the realization of the company's system policies and objectives, and meeting the requirements of relevant parties.
--Quality Analysis
The company comprehensively collects, organizes, and measures product quality data and information through various channels such as statistical caliber, financial statements, and special meetings, analyzes the data and information, and formulates corresponding improvement measures.
3. Operation Management
a) Product Design Integrity Management
The company's product design and R&D strictly control the entire process related to R&D, from R&D project initiation to various activity records during the process, R&D process summary, and management evaluation.
b) Integrity Management of Raw Material or Component Procurement
The company classifies materials into three categories (A, B, and C) based on the risk level of the materials to product quality. For Category A material suppliers, in addition to meeting the legally required qualifications, on-site audits must also be conducted regularly. For Category B material suppliers, the company must first conduct a risk analysis of the material and decide whether an on-site audit is needed based on the quality of the materials provided by the supplier. For Category C material suppliers, generally only their qualifications are considered. After the company conducts qualification audits and on-site audits of material suppliers, material suppliers that meet the requirements and are approved for procurement will have quality files established. All purchased raw materials are subject to 100% inspection, and any raw materials that do not meet the specified standards are not allowed to be stored or used.
Regarding the procurement of equipment and components, the relevant qualifications of suppliers are strictly reviewed. When purchasing equipment and components, standard parts are purchased and used whenever possible; for parts requiring special processing, the usage effect must be fully verified to ensure that they meet the company's requirements. All equipment must undergo equipment verification before use to ensure that it meets product process requirements.
c) Integrity Management of Production Processes
The company's production department and technology department are specifically responsible for the production management and technical management of various products. Various production management systems, work standards, job operating procedures, and various process procedures, management procedures, and standard operating procedures have been formulated and gradually improved. On-site training in the workshop and pre-shift/post-shift meetings are used to provide comprehensive job skills training to operators at various positions, requiring certification before assuming their positions. Various methods are used for supervision and assessment to enhance employees' quality awareness and improve operational skills. During the production process, managers at all levels strictly fulfill their management responsibilities, conduct timely inspections, and promptly correct errors to ensure stable production order.
Before adding materials, the raw materials, auxiliary materials, and packaging materials required for production are reviewed to ensure the quality of intermediate products and finished products. The "three no" principle of "no production, no acceptance, no transfer" is strictly enforced for non-conforming products. Quality control points are set up for key processes to urge employees to perform self-inspection, mutual inspection, and special inspection work. The management procedures for batch records are strictly followed to ensure that the receipt, issuance, and verification are unified. Material balance is performed for each production step to ensure that the input of materials and the output of products are consistent with the process requirements, confirming that there are no potential quality hazards.
Production records are reviewed and kept by the production department, and special forms are designed by the technology department and uniformly printed by the company. Employees must fill out production records promptly as required, ensuring that the handwriting is clear, the content is true, the data is complete, and the operator and reviewer sign for confirmation. After each batch of production is completed, the workshop statistician summarizes and reviews the records, promptly submits them to the production department, and after review and confirmation, organizes and files them by batch number, managed by a designated person.
Based on industry characteristics and actual conditions, the company strengthens the level of information construction in the production process, implements systematic management of the entire production process, taps internal potential, leverages the strength of technical backbone personnel, conducts continuous improvement or technological innovation of existing equipment, and conducts technological breakthroughs on weak links; production employees must undergo training and assessment before taking up their positions, establishing personnel training files, and using various methods such as centralized training, pre-shift meetings, "passing on, helping, and guiding," and visualization to enhance their work skills and quality awareness. Production employees strictly abide by workshop discipline.
The company implements a lean production organization model to shorten production and delivery cycles, quickly adapt to the fluctuations in the variety and quantity of market orders, meet customer needs while reducing inventory, and enable customers to fully understand the performance of jade beds (mattresses) and further recognize product quality. The order rate has also increased, and to a large extent, after-sales quality problems have been solved, reducing the workload of after-sales service personnel and making after-sales service arrangements more flexible.
4. Marketing Management
According to strategic requirements, the company segments the market to improve the effectiveness and targeting of resources and operations. Determine customer needs and expectations for different types of customers, determine appropriate methods based on their needs and expectations, establish corresponding systems and teams, establish various channels and methods, and specifically understand customer needs and expectations.
The company understands customer needs and expectations through channels such as exhibitions, industry conferences, industry standard committees, public media, the Internet, and external organizations, using methods such as questionnaires, face-to-face or telephone interviews, observation inquiries, and external commissioning.
Various departments of the company regularly collect customer information, analyze it, and classify and summarize the determined customer needs information according to different market segments, forming a database of needs and expectations for different customer groups, and summarizing the overall needs characteristics of different market segment customer groups from it, which is used as a reference for product planning, product development and design, and process control decisions.
With the core values of "diligent learning, pioneering innovation, and pursuing a healthy and beautiful life," the company promotes the implementation of the talent plan, requiring all employees to diligently learn and bravely pioneer and innovate in their work. For any customer (or agent), regardless of whether they place an order, they must be enthusiastic and considerate and try their best to meet all their reasonable needs, increasing the skills and quality of business personnel from various aspects and improving the customer closing rate.
The company establishes a customer return visit system, adopting a voluntary customer form, recording relevant information such as the customer's contact number and order time, and conducting telephone return visits after a period of time (usually within one year) to improve customer satisfaction.
The company establishes a rapid response mechanism for timely feedback and handling of user complaints. The response time for complaints/emergency handling is generally no more than one day, and timely countermeasures are taken for unpredictable changes.
(5) Corporate Culture Construction
1. Vision, Mission, Values
Table 2: The company's quality philosophy
Item Contents |
In Content |
mission |
Improve public sleep quality, promote technological progress, create social value, and achieve corporate profits |
Vision |
To be the leader in intelligent, warm, and functional bedding |
Core Values |
diligent learning, pioneering and innovating, pursuing a healthy and beautiful life |
business philosophy |
Truth-seeking, pragmatism, trustworthiness, and innovation |
- Mission: Improve public sleep quality, promote technological progress, create social value, and achieve corporate profits
The mission carries social responsibility and obligations. Fukido Company's products are mainly used to improve the sleep quality of the public. With good sleep quality, people are healthy and energetic to work and live, each contributing to society through their own efforts, while enjoying the comfortable life that society brings to people.
Fukido products are reliable in quality and high in technology content, and are recognized and favored by the public, reflecting the company's social value and the technological progress of the products. Through product market access and customer recognition, corporate profits have increased significantly.
- Vision: To be the leader in intelligent, warm, and functional bedding
Being an industry leader has always been the company's beautiful vision. When doing business and making products, we must make technologically leading products.
Therefore, while ensuring the technological content of the products, creating high-tech products that meet people's needs and are at the forefront of the times can allow the company to remain invincible. Therefore, Fukido Company is constantly developing and researching new products, introducing advanced technologies, and leading the industry in high-end intelligent warm products.
③ Core Values: Diligent study, pioneering innovation, and the pursuit of a healthy and beautiful life
Diligence and dedication reflect the value of life. To be diligent, one must constantly strive to learn, and through the continuous accumulation of new knowledge and experience to better expand thinking, pioneer innovation, and realize the lofty ideals of life.
2. Brand Building Status
Jiaxing Fukido Temperature Control Bed Co., Ltd. has won market reputation with product quality, has a good brand image in the industry, its products have high recognition in the industry, and its products and services are recognized by users. In the past three years, customer satisfaction has been on the rise. The company's performance results in terms of customers and markets, including customer satisfaction, show that Fukido products remain at a high level.
The company continues to expand its "refined, specialized, and new" R&D team, continuously improving product technology levels and quality performance. In the past three years, products have been repeatedly recognized by customers and peers.
Table 3: Performance Results Related to Quality Management Level
Index Item |
Unit |
2022 |
2023 |
2024 |
Customer Satisfaction |
% |
96.2 |
96.5 |
97 |
(VI) Enterprise Product Standards
1. Standard Implementation
Fukido Company has always strictly implemented national standards in product design and management. Typical standards include GB/19001-2016 Quality Management Systems Requirements, CNCA-00C-005 Mandatory Product Certification Implementation Rules Factory Quality Assurance Capability Requirements, CNCA-C07-01-2017 Mandatory Product Certification Implementation Rules Household and Similar Purpose Equipment, etc.
2. Patent Status
In the past five years, the company has obtained 1 invention patent authorization, 51 utility model patent authorizations, and 25 appearance patent authorizations.
3. Product Inspection Standards and Levels
The company implements enterprise standardization throughout the entire production process, establishing relevant standards for all aspects, from the procurement of raw and auxiliary materials and packaging materials to semi-finished and finished product inspections. This ensures that the entire production process, from the entry of raw and auxiliary materials to the delivery of finished products, is under standardized and normative management, laying a solid foundation for stabilizing product quality and improving enterprise management levels.
Table 5: Performance Results Related to Quality Management Level
Index Item |
Unit |
2022 |
2023 |
2024 |
Raw Material Incoming Inspection Pass Rate |
% |
99 |
99 |
100 |
Workshop First Inspection Pass Rate (Average) |
% |
98.5 |
98.5 |
98.4 |
Delivery Completion Rate |
% |
99.5 |
99.6 |
92.5 |
Customer Complaint Rate |
% |
0 |
0 |
0 |
4. Product Quality Level
Since its establishment, the company has never experienced any major quality complaints, and the pass rate has reached 100% in annual inspections by various levels of quality and technology departments.
(VII) Enterprise Metrology Level
The company strictly implements documents and regulations such as the "Measurement Law of the People's Republic of China", establishing a complete set of management documents and control methods from raw material procurement, process management, production equipment, inspection equipment, process inspection, and finished product inspection. Specialized and part-time metrology personnel are responsible for the management, configuration, and regular calibration of the company's in-use measuring equipment. Emphasis is placed on professional training for metrology management personnel, providing strong support for the standardization of the company's metrology management.
To ensure product quality, strict process control is implemented in the product production process, and metrology management is strengthened for raw and auxiliary materials in the production process to ensure the normal operation and accuracy of measuring equipment.
For measuring instruments, procurement, warehousing, and outbound procedures are strictly implemented in accordance with the approved plan and management procedures. The warehouse has dedicated personnel to manage measuring instruments, establishing account books and registration procedures. The use of measuring instruments must pass verification, and only those with a valid verification certificate can be put into use; in-use measuring instruments are strictly calibrated according to the cycle, strengthening on-site inspections and supervision, understanding their usage, and addressing problems promptly; putting forward improvement suggestions for problematic departments, taking positive and effective measures for rectification, and laying a solid metrology foundation for the production of high-quality products.
Table 7: Testing Equipment Used by the Company
Equipment |
Name |
Model |
Origin |
Quantity |
Advanced Level |
Main Detection Equipment |
Multi-channel Temperature Tester |
TC1008 |
Hangzhou Weibo Technology Company |
1 |
Advanced |
Automatic AC Voltage Stabilizer |
TDN1-3 |
Zhejiang Zhengtai Electric Co., Ltd. |
1 |
Advanced |
|
Leakage Tester |
LK2675 |
Changzhou Blue Light Electronics |
1 |
Advanced |
|
Leakage Current Tester |
WB2675A |
Hangzhou Weibo Technology Company |
2 |
Advanced |
|
Electrical Parameter Tester |
PF120E |
Hangzhou Weibo Technology Company |
3 |
Advanced |
|
Withstand Voltage Tester |
WB2672A |
Hangzhou Weibo Technology Company |
3 |
Advanced |
|
Ground Resistance Tester |
KC2678A |
Hangzhou Kunce Technology Co., Ltd. |
1 |
Advanced |
|
Infrared Thermometer |
DE6830B |
Delixi Electric Co., Ltd. |
1 |
Advanced |
|
Wood Testing Instrument |
PT90B |
Shanghai Xin Jie Electronics Co., Ltd. |
1 |
Advanced |
|
|
|
|
|
|
(8) Certification and Accreditation Status
Currently, the company has passed ISO9001 quality system certification, GBT14001, and GBT45001 environmental and occupational health enterprise qualification acceptance, and is preparing to accept the "Zhejiang Manufacturing" brand certification. The company will strictly control the quality of its products according to international quality management system standards to ensure the quality of its products, thereby enabling the company's quality policy of "pursuing excellence, scientific innovation; customer satisfaction, continuous improvement" to be successfully implemented.
--Management System
Fuxiduo Company has passed ISO9001, GBT14001 and GBT45001 three-system certifications, and its products have reached the advanced level in the industry.
(9) Product Quality Commitment
The company provides perfect after-sales service to protect the interests of customers. The company has established a "Customer Complaint Handling Procedure" 24 hour complaint hotline, answering and handling customer complaints around the clock. The marketing department's after-sales service department is responsible for handling customer complaints and repair complaints. 2 must respond within hours; if it cannot be handled on-site, explain the situation to the customer, return to the company to gather relevant technical personnel to analyze the cause, formulate a solution, and strive to solve the problem within 3 days; if it still cannot be solved, it will be treated as a special case, and the company will organize special forces to tackle the problem to ensure customer satisfaction. For major complaints, the company's quality inspection, technology, manufacturing, quality assurance, and marketing centers will jointly discuss solutions and improvement measures, and generally can solve the problem within one week.
(10) Quality Complaint Handling
The company establishes and implements a customer complaint handling process to ensure timely and effective handling of customer complaints. Customer complaints are handled by dedicated personnel. Each complaint form is closely monitored. Based on the differences in the type and degree of customer complaints, focusing on the customer and paying attention to collecting and resolving customer feedback, necessary corrective/preventive measures are taken to prevent the recurrence of similar problems. The complaint handling process is tracked through telephone follow-up to understand customer satisfaction.
The company's quality department regularly monitors customer complaint information, and the after-sales service department collects and analyzes problems that repeatedly occur in the market and affect customer satisfaction and product experience, and generates reports. Regularly organize internal company departments to hold product quality meetings. Establish quality control circles, cross-departmental product quality improvement teams, and simultaneously coordinate with upstream suppliers and related partners to tackle and improve major product quality problems, eliminate quality risks, and improve product quality satisfaction.
(11) Quality Risk Monitoring
The company formulates a routine product production operation control process, strictly controlling each link and strictly controlling it to ensure that the production of each part meets the relevant requirements and ensures the final product quality is qualified. The company also uses the "three inspections ” system, namely self-inspection, mutual inspection, special inspection, to strictly control product quality. Self-inspection includes 了 product the entire production process employees inspect the products they produce according to the drawings and technical requirements, make a judgment on whether they are qualified, and make inspection records make relevant self-inspection records. Then, the product manufacturing process is inspected by the team leader and the professional inspector. Only when the process quality is qualified can the next process be carried out. The modular production model makes product key quality links exposed and controlled, thereby ensuring product quality and safety , preventing quality and safety risks 。
The company has formulated a quality control system, with the general manager as the highest quality person in charge, clarifying the quality control system structure and the responsibilities of each relevant department.
III. Outlook
For many years, we have unswervingly followed the development path of win-win cooperation, carrying out all-round and multi-form joint ventures and cooperation with many excellent partners, learning in cooperation, improving in cooperation, and pursuing long-term development and mutual benefit and win-win results. We believe that through wise union and team collaboration, we will achieve complementary advantages and write the grand blueprint of "National Brand, World Fuxiduo".